Having so many issues learning illustrator from online tutorials! They
seem to speak in illustrator which is rather annoying- 'let me just
vector that' or whatever. WHAT DOES IT MEAN?! So literally have to do
the 'Illustrator for beginners' ones which do not look as cool as the
other ones :( Also, the American accents are really starting to grate.
S'all I'm saying.
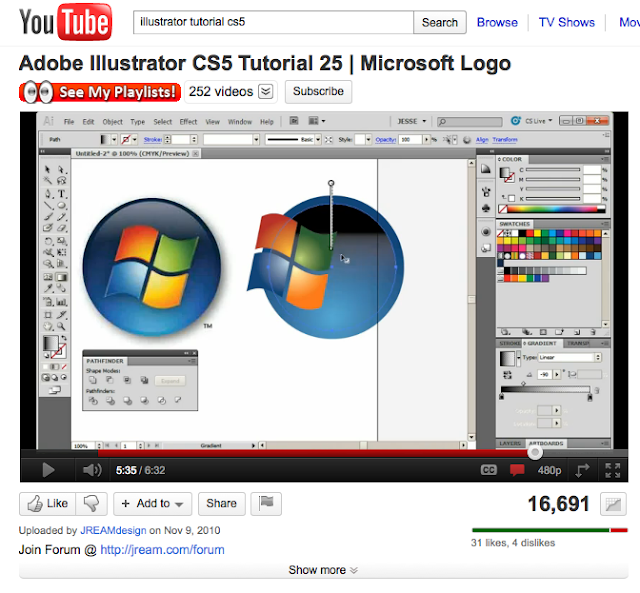
This one seemed really cool but again, too difficult for my meager skills.
Tried to search for 'beginners Illustrator' but all the videos that came up were just of the pen tool (which have got a vague grasp of) and making shapes.
HA! Just had a look on google with 'illustrator tutorials' and this woman says she can teach you...in 23hours 12 minutes. Oh but you can only look at them if you give her money. Bad luck really, was so looking forward to that day of Illustrator. Rats.
Ok this really isn't going to work- I don't understand the tutorials as my illustrator is COMPLETELY DIFFERENT. Where are they getting all these little pop ups from?!
Next plan of action- written tutorials...
Found this one which looks vaguely do-able
Am totally gonna nail this shell thing.
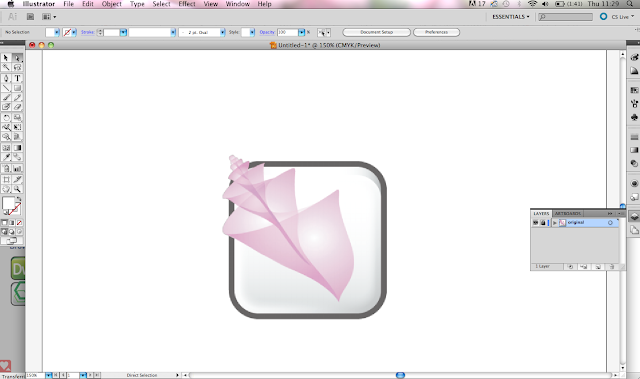
Ok so I imported a picture I found on google of the same Adobe Bridge shell logo, made it my layer 1- put 50% invisibility on it...its all going very well.
Started then to use the Pen Tool to make the shell. Not as easy as first envisaged. Am rubbish at pen tool it turns out, but it doesnt really matter- will use that white clicker thing to change all my angle points. PLAN.
Mine doesn't look too similar to the lady's shell but figure it will all be ok as at the end hers does not even have a black outline. Maybe we delete it later?
And this is where I came to an abrupt halt. After nearly 3/4 of an hour carefully outlining a shell I cannot understand what she means with '2 colour radial gradient'. I'm not entirely sure where I put the two colours to make up a gradient. Might ask one of the IT tekkies to help me. I tried, just to put some colour into it, to do the 'fill' but turns out Illustrator not only has no 'fill' button (or if it does- where is it?!) but I cannot seem to group the first layer of lines together. I literally have anger in my heart for this programme.